お客様の課題
従来4,000ショット程度で交換
焼付や溶損で非常に困っている部品の改善相談を受ける
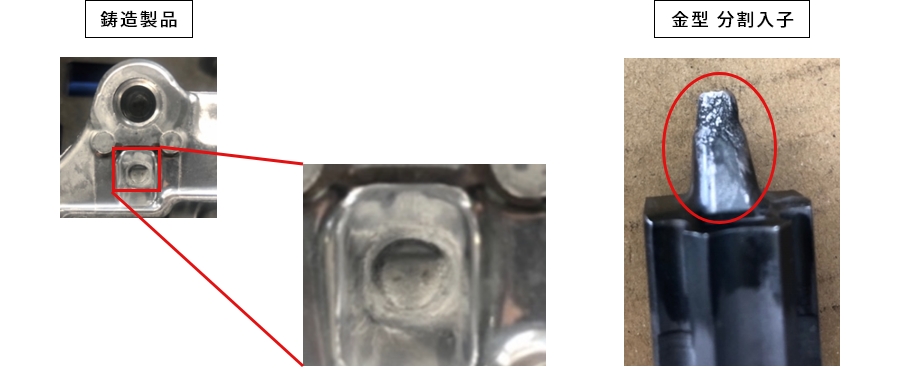
左の写真は鋳造製品の状態です。
右の写真は金型分割入子の状態となります。
いずれも鋳造開始後4,000Sの状態を示しており、金型側の焼き付き・溶損が激しく形状を維持できていないため、製品に影響が出てしまっています。
従来のドリル加工では、金型側の先端形状部位に十分な冷却機構が設置できないため部品の短寿命という結果に繋がり、それを交換するためのメンテナンス手番がかさみ量産効率に悪影響を及ぼしています。
鋳造品・図面・部品での状況確認
通常のドリル加工水穴では、浅く設定するしか手段が無い。
結果、冷却効果が低く部品寿命に大きく影響している。
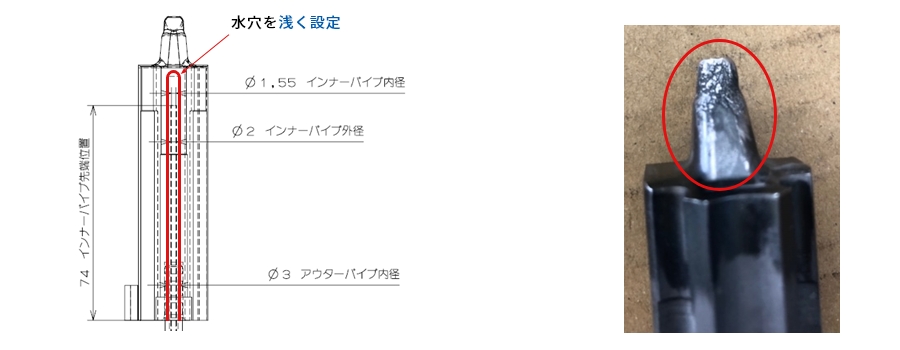
金属3Dプリンタによるコンフォーマルクーリングの提案
- ・通常のドリル加工では不可能であった、金型製品部表面に沿った内部形状冷却をデザイン
従来より深く水穴を設定することで放熱面積を広げた仕様に変更。大きな冷却効果が期待でき、焼付や溶損対策になる。 - ・4,000ショットで廃棄していた製品を預かり、消耗部分(製品部)をカット、新規水路で造形実施
廃棄予定の入子の先端部のみを改造しているため、新作するよりイニシャル・ランニング共にコスト低減できる。
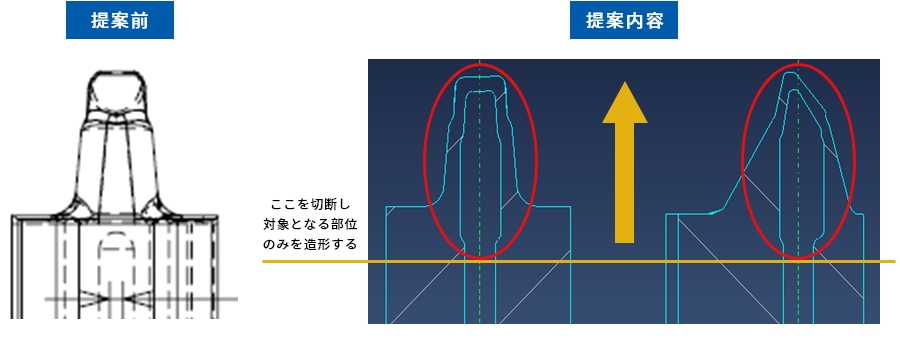
これまでのドリル加工では不可能であった、「3D形状型 内部冷却機構」をデザインし放熱面積を広げる仕様への変更です。
これにより冷却効果の向上が期待でき、焼付き・溶損の対策ができます。
そして、もうひとつは、コスト低減です。
従来4,000Sで廃棄していた入子を提供いただき、形状冷却の対象となる部位のみを切断して造形による改造を行うことで丸々新作ではなく、改造のみのコストで済むという内容です。
金属3Dプリンタによるコンフォーマルクーリングの評価
鋳造品を見比べれば歴然
4,000ショットで交換していた《改善前》の部品は《改善後》40,000ショット到達
鋳造品の品質向上・金型メンテの手番削減・部品の寿命が大幅にのびた。
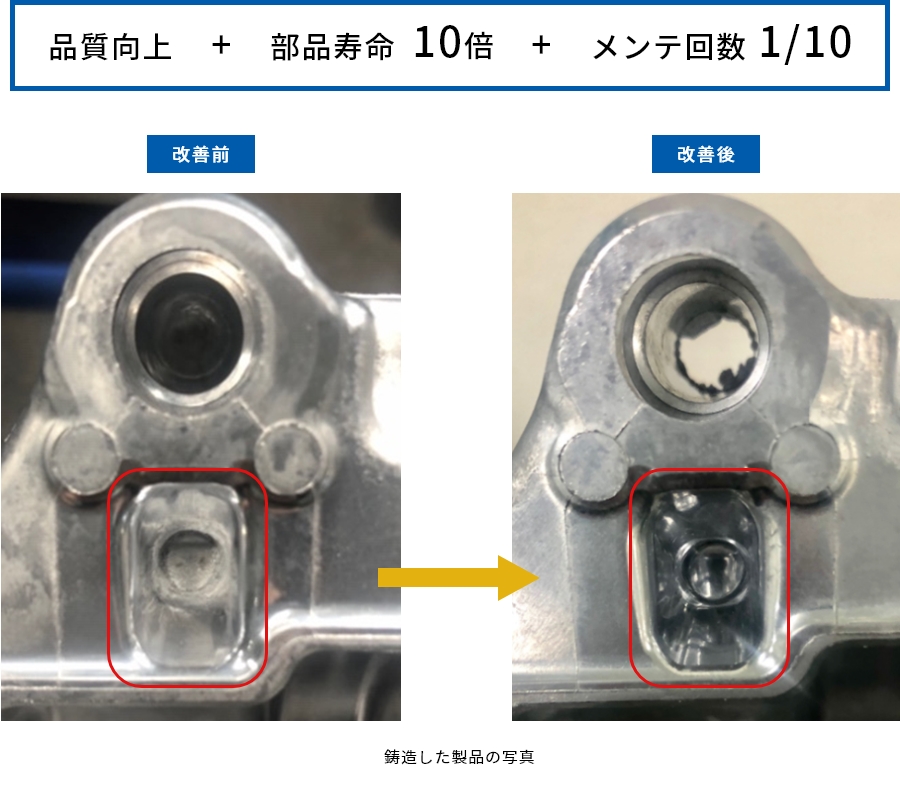
非常に良好な結果を得た為、別部品も同様に切替検討頂くことになった。
鋳造製品の品質向上は歴然。
また、金型部品の寿命についても10倍の40,000Sまで伸びました。
これにより、メンテナンス回数も1/10となり手番削減にもつながりました。
積層造形入子の製作費用は、通常鋼材を切削製作する従来品と比較して約2~3倍と決して安価ではありませんが、寿命の向上とメンテナンス回数の低減というランニングの視点で捉えると、その効果は歴然と言うことが実証できました。
利用サービス
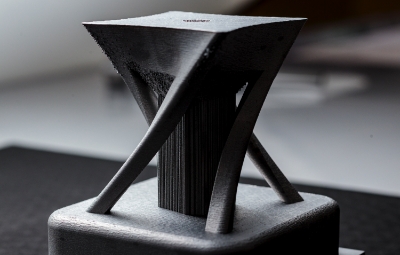